In 2024, the digital revolution continues to reshape the manufacturing landscape, presenting challenges and opportunities. Join us as we explore the five crucial steps to digitize your manufacturing workflow effectively. From leveraging data and IoT to optimizing processes and enhancing collaboration, we’ll guide you through the journey of modernizing your operations and staying ahead in the competitive market of tomorrow.
5 Steps To Digitize Manufacturing in 2024
Step 1: Enhance insight into production processes using live data analysis
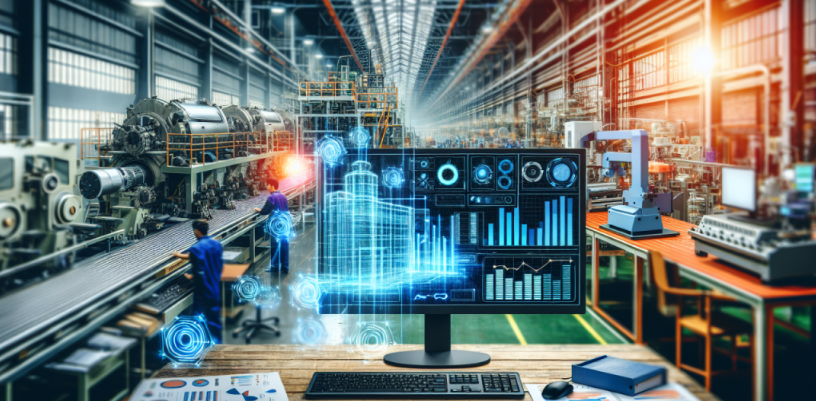
Enhance the production process via data analytics
Real-time analytics in manufacturing brings digital advancements that offer enhanced visibility into production processes. Enabling real-time monitoring and analysis of production activities facilitates the identification of potential issues, thus facilitating proactive measures to mitigate downtime and disruptions.
Furthermore, real-time analytics provide valuable insights into production efficiency, aiding in understanding customer demand and optimizing supply chain performance.
Numerous approaches can be adopted to implement real-time analytics and improve visibility within manufacturing:
- Deploy an Enterprise Resource Planning (ERP) System:
ERP systems automate and streamline manufacturing processes, offering comprehensive visibility across production operations and real-time data analysis.
- Utilize a Manufacturing Execution System (MES):
MES software monitors, records, and optimizes production processes, providing both real-time visibility and in-depth analytics, fostering further digitization in manufacturing.
- Integrate IoT Solutions:
Internet of Things (IoT) solutions enable real-time monitoring of machinery, production tracking, and data collection, facilitating the generation of actionable analytics.
- Harness Predictive Analytics and Machine Learning:
Leveraging predictive analytics and machine learning enables real-time data analysis, allowing for the proactive identification of issues and optimization of production processes.
Step 2: Mitigate asset and process failures through predictive analytics
In the digital transformation of manufacturing, predictive analytics emerges as an important tool alongside real-time analytics, aiding companies in optimizing operations and enhancing efficiency.
Predictive analytics detect patterns and forecast future outcomes by harnessing current and historical data. This analytical approach empowers manufacturers to foresee demand, ensure quality standards, trim expenses, and explore avenues for expansion.
Furthermore, predictive analytics pinpoints areas ripe for enhancement within the production cycle, enabling manufacturers to boost output and minimize wastage. Additionally, it uncovers prospects for automation, allowing companies to trim labor costs while enhancing precision and speed. Through the integration of predictive analytics in manufacturing digitization, a deeper understanding of the business landscape is achieved, ensuring a competitive edge.
Step 3: Enhance inventory control via digital transformation
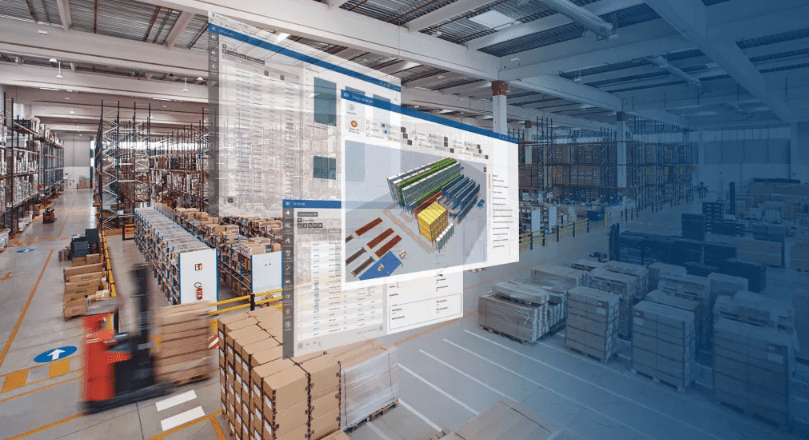
Control inventory management through data
In 2023, the worldwide market size for inventory management software reached $2.13 billion and is expected to rise to $2.31 billion in 2024, with a substantial increase to $4.84 billion by 2032. This raises the question of why inventory management holds such significance within the digitalization and digitization processes undergone by the manufacturing industry.
Digitalization within manufacturing aids in optimizing inventory levels and expenses, thereby minimizing waste and enhancing order precision. This includes overseeing the movement of materials and goods throughout the production cycle. The objective of inventory management is to guarantee the availability of appropriate quantities of materials and products at the precise moment required to fulfill production requirements. Implementing an effective manufacturing execution system is among the digitalization facets that can bolster inventory management endeavors.
Step 4: Enhance manufacturing accuracy through quality assurance
Utilizing digitalization, manufacturers can quickly and accurately identify product quality issues to prevent further setbacks. Automated quality assurance, integral to digitization in manufacturing, offers various functionalities, including product inspection, testing, and analysis, ensuring adherence to required standards. Typically, such systems comprise sensors, actuators, and controllers.
Sensors detect anomalies in the production process and prompt the controller to enact corrective measures. Actuators execute these measures, such as halting production or adjusting processes. The controller makes decisions based on data gathered by sensors and actuators. These components are interconnected within the manufacturing process, underscoring the necessity of digitization and digitalization for their integration.
Step 5: Streamline supply chain operations
Through digital transformation, manufacturers can streamline their supply chains, cutting inventory expenses, enhancing turnaround times, and boosting manufacturing facility efficiency while reducing material wastage.
Furthermore, optimizing supply chains through digitalization brings forth additional advantages. It enables manufacturers to gain insights into their supply chains, facilitating the identification of risks, the mitigation of disruptions, and the management of supplier relationships. This interconnectedness underscores the multifaceted relationship between manufacturing and digitization.
Leverage CMC Global for Manufacturing Digitalization and Digitization
The successful manufacturing process digitalization lies in the technical proficiency offered by your technology partner. Collaborating with a dependable manufacturing software development company can empower your enterprise by crafting bespoke solutions tailored to your unique requirements.
CMC Global aids clients in achieving manufacturing digitization by delivering a comprehensive array of services, ranging from bespoke software development to the integration of cutting-edge technologies and tools like Computer Vision, Big Data, AI, and Machine Learning, among others. Our team boasts extensive expertise in engineering, Robotic Process Automation, and industrial solutions.
Our experts excel in creating digital replicas of physical objects for simulating production processes, devising predictive maintenance solutions, and automating workflows through machine learning algorithms. Additionally, we offer pioneering solutions encompassing data visualization, deep learning, IoT, and Embedded software.
Contact us for a free consultation and further details!
